Lean metode su set principa i tehnika usmerenih na eliminaciju rasipanja (gubitaka) i kontinuiranog poboljšanja poslovnih procesa. Ove metode potiču iz Toyota proizvodnog sistema i danas se primenjuju u različitim industrijama.
Osnovni principi Lean metodologije su:
- Definisanje vrednosti – Razumevanje šta kupac stvarno vrednuje i eliminacija aktivnosti koje ne dodaju vrednost
- Mapiranje toka vrednosti – Analiza svih koraka u procesu kako bi se identifikovala i eliminisala rasipanja
- Nesmetan protok meterijala i informacija – Optimizacija procesa kako bi se eliminisala kašnjenja i prekidi u radu
- Povlačenje – Proizvodnja ili isporuka samo onoga što je potrebno i u količini koja je potrebna, kako bi se smanjili zalihe i gubici
- Težnja ka stalnim poboljšanjima (Kaizen) – Neprekidno poboljšavanje procesa kroz male, ali stalne promene
Obzirom da su Lean metode usmerene na eliminaciju rasipanja, potrebno je definisati najčešće vrste rasipanja koje se sa uspehom rešavaju primenom Lean metoda:
- Prekomerna proizvodnja – Proizvodi se više nego što je potrebno
- Zalihe – Držanje prevelikih zaliha koje vezuju kapital
- Krtanje – Nepotrebno kretanje radnika ili opreme
- Transport – Nepotrebno premeštanje materijala ili proizvoda
- Čekanje – Gubljenje vremena zbog kašnjenja u procesima
- Prekomerna obrada meterijala i informacija – Izvršavanje više posla nego što je potrebno
- Defekti – Greške koje dovode do dorade ili škarta
Za prevazilaženje problema i smanjenje rasipanja koriste se Lean metode i alati u skladu sa Lean planom.
Lean plan se razlikuje da li se radi o proizvodnji ili uslugama, razlikuju se takođe i od vrste proizvodnje, da li je serijska ili pojedinačna proizvodnja.
Radi lakšeg razumevanja lean plan je prikazan na primeru proizvodnje metalnih konstrukcija.
Lean plan za proizvođače metalnih konstrukcija sadrži nekoliko faza:
1. Analiza trenutnog stanja (Value Stream Mapping - VSM)
Prvi korak je mapiranje toka vrednosti od sirovina do gotovog proizvoda:
- Nabavka materijala
- Sečenje i obrada metala
- Zavarivanje i montaža
- Kontrola kvaliteta
- Transport i isporuka
Identifikacija problema se odnosi na:
- Nabavka traje 2 dana, u magacinu nije jasno definisano kolike su minimalne zalihe – rasipanje je Čekanje na materijale → rešenje ovog problema primenom Lean metode – Optimizacija nabavke (Just-In-Time).
- Višak zaliha gotovih zavarenih elemenata za montažu – rasipanje prostora i uticaj na kvalitet proizvoda zbog neadekvatnog skladištenja, povećanje troškova zbog zaštite u međuskladištu → rešenje ovog problema – Smanjenje skladištenja kroz Pull sistem.
- Defekti i ponovni radovi, kontrola je ustanovila da je 12% komada urađeno sa greškom od čega je 5% moguće doraditi, a 7% je škart – radi se o rasipanju troškova u pogledu materijala i vremena dorade → Rešenje ovog problema – Poka-Yoke sistemi za prevenciju grešaka.
- Neefikasno korišćenje radne snage, raspored radnih mesta, skladišta alata i međufazna skladišta takvog rasporeda koje zahteva stalno kretanje radnika, transport materijala internim transportom, čekanje radnika na sledeću operaciju – Rasipanje troškova, rasipanje vremena, rasipanje enrgije radne snage… → rešenje ovog problema – Lean layout i standardizacija rada.
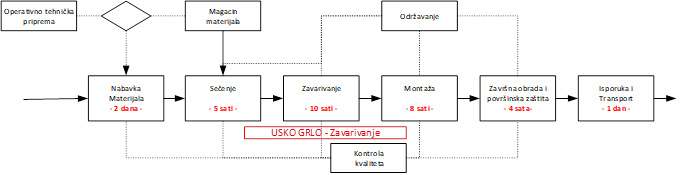
2. Eliminacija rasipanja i povećanje efikasnosti
Najčešća rasipanja prema Lean metodologiji se mogu svrtati u 7 tipova rasipanja:
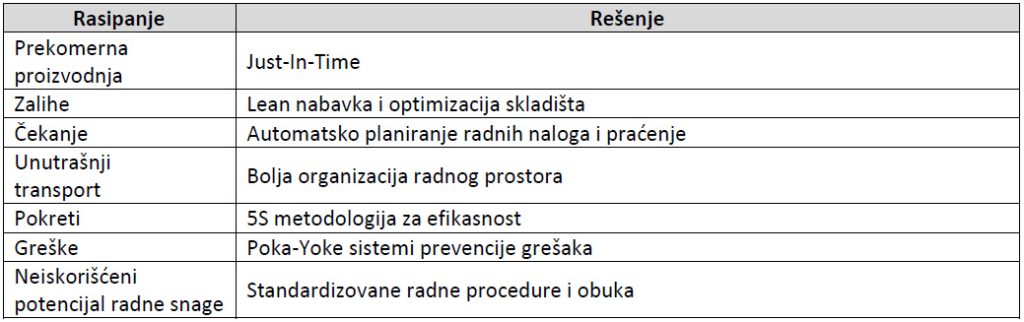
3. Implementacija Lean Alata
5S Metodologija
- Sortiraj: Ukloniti nepotrebne alate i materijale iz radnog prostora
- Sredi: Optimizovati raspored alata i materijala za lakši pristup
- Uglancaj: Održavati radne površine čistima i bez otpada
- Standardizuj: Uspostaviti jasne procedure za organizaciju radnog mesta
- Održavaj: Redovno kontrolisati i unapređivati sistem
Just-In-Time (JIT) Proizvodnja
- Nabavljati materijale po potrebi kako bi se smanjile zalihe
- Implementirati Kanban sistem za signalizaciju potreba u proizvodnji
- Uskladiti proizvodne kapacitete sa realnim zahtevima kupaca
Standardizacija Rada
- Kreirati standardne operativne procedure (SOP) za svaku fazu proizvodnje
- Definisati optimalne metode zavarivanja i montaže
- Obučiti radnike za primenu Lean principa
Poka-Yoke (Prevencija Grešaka)
- Implementirati alate i šablone koji sprečavaju pogrešnu montažu.
- Koristiti senzore i vizuelne signale za kontrolu kvaliteta.
Total Productive Maintenance (TPM)
- Planirati redovno preventivno održavanje opreme kako bi se smanjili kvarovi.
- Obučiti operatere da prepoznaju znakove habanja i oštećenja.
4. Kontinuirano Poboljšavanje (Kaizen)
Uvođenje Kaizen kulture
- Organizovati mesečne Kaizen sastanke sa radnicima radi identifikacije poboljšanja
- Uspostaviti sistem nagrađivanja za predloge za optimizaciju
- Definisati ključne pokazatelje performansi (KPI) i pratiti ih.
Vizuelni Menadžment
- Postaviti sistem za signalizaciju problema u proizvodnji
- Koristiti grafičke prikaze za praćenje produktivnosti i defekata
5. Očekivani Rezultati i Benefiti
Tipični očekivani benefiti i vidljivi rezultati nakon provođenja optimizacije procesa kroz primenu Lean metodologije su:
- Smanjenje vremena nabavke materijala i optimalnije skladištenje
- Smanjenje vremena proizvodnog ciklusa rešavanjem uskih grla u proizvodnji
- Smanjenje troškova skladištenja i škarta
- Poboljšanje tačnosti isporuke kupcima
- Povećana produktivnost, motivacija i moral radnika
- Smanjenje grešaka i dorada
6. Dinamički plan implementacije Lean metodologije u proizvodnji
Na kraju pripreme za primenu lean metodologije u proizvodnji definiše se dinamički plan koji treba da rezultira dostizanjem rezultata u smanjenju rasipanja koj smo identifikovali. Primer dinamičkog plana implementacije je dat u tabeli 2.

Osim navedenih aktivnosti u planu, početna obuka i angažovanje tima za optimizaciju ključni su faktori uspeha u implementaciji Lean sistema.
Striktno poštovanje Lean plana, posebno u stavki analize, je preduslov da se utvrde rasipanja i preduzmu koraci na njihovom rešavanju. Ako analiza pokaže da su rasipanja prisutna na više mesta, tada rukovodstvo može zahtevati da se svakom procesu i rasipanju unutar njega pristupa pojedinačno, tj da se deluje manje frontalno.
Implementacija Lean metodologije na smanjenju rasipanja je vrlo praktičan način da se kompanija pokrene od strane svih zaposlenih koji su motivisani da učestvuju u optimizaciji procesa u kome su angažovani. Sa druge strane realizacija Lean plana omogućava kompaniji da smanje troškove, poboljšaju kvalitet i povećaju konkurentnost na tržištu.